The success of the gramophone to play recorded sounds was dependent on the ability to mass produce records.
The process of making records has its roots in Thomas Alva Edison’s phonograph. First, a master recording is made, usually in a studio where engineers perfect the recorded sound. Then an object called a lacquer is placed on a record-cutting machine, and as it rotates, electric signals from the master recording travel to a cutting head, which holds a stylus, or needle. The needle etches a groove in the lacquer that spirals to the center of the circular disc. The imprinted lacquer is then sent to a production company.
There, the lacquer is coated in a metal, such as silver or nickel, to produce a metal master. When the metal master is separated from the lacquer, the resulting disc has ridges instead of grooves. The metal master is then used to create a metal record, also called the mother, which is then used to form the stamper. Stampers are just negative versions of the original recording that will be used to make the actual vinyl records.
Next, the stamper is placed in a hydraulic press, and vinyl is sandwiched in between. Steam from the press softens the plastic as the stampers push an impression of the master recording onto it. Finally, the disc is stiffened using cool water. (Read more)
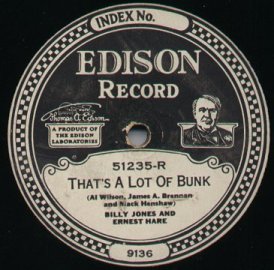
The micro-groove or long-playing record technology built on advances that been available, but unused since the 1930s. By this point the big record companies realized that creating a longer-playing record would require a tougher medium that could hold a smaller groove. They would also require more sensitive electromagnetic pick-ups that would not rapidly wear down the records.
The type of recording medium was the first crucial aspect. Earlier attempts to produce a long-playing record had failed because slower turntable speeds on shellac records resulted in more “rumble” and unwanted undesirable frequency noise. Record companies had tried and failed to add more grooves to records to increase their playing time, but the shellac surface could not effectively hold all of the sound information of the smaller grooves. One of the major advances that had been made in the 1930s was the introduction of vinyl resins. These records consisted of mixture of vinyl chloride and vinyl acetate, known as Vinylite, which was harder and finer than shellac, and allowed the discs to be cut with 224 to 226 grooves per inch, which was a massive improvement over the former 80 to 100 grooves per inch. Decreasing the width and increasing the number of grooves was only one of the ways to make records play longer. The other was to slow down the rate of revolution on the turntable. Throughout the 1930s many companies tried one or both of these techniques to create a longer-playing record, but Columbia was first to successfully combine both of these methods to create a long-playing record. (Read more)
Once the record is ready to be played, it will need a proper machine to bring its sounds to life. To learn how records are played, see next page.